Installing IPC cable clamp is a critical task that demands precision and adherence to safety protocols. Poor installation practices can lead to electrical failures, safety hazards, or long-term system vulnerabilities. This guide outlines key precautions to ensure reliable, safe, and efficient IPC installations.
Pre-Installation Checks
1. Verify Cable and Connector Compatibility
Match Design Specifications: Confirm that the main and branch cables align with project drawings.
Inspect IPC Specifications: Ensure the clamp’s voltage rating, material, and size match the design requirements.
2. Assess Cable Condition
Check for Moisture: Ensure cables (especially cores) are dry to prevent short circuits.
Evaluate Stripping Dimensions: Follow manufacturer guidelines for insulation stripping lengths and avoid damaging inner layers.
3. Prepare the Worksite
Maintain Cleanliness: Dust or debris can compromise connections. Clean the area thoroughly.
Control Environmental Factors: Minimize exposure to humidity, extreme temperatures, or contaminants.
Installation Best Practices
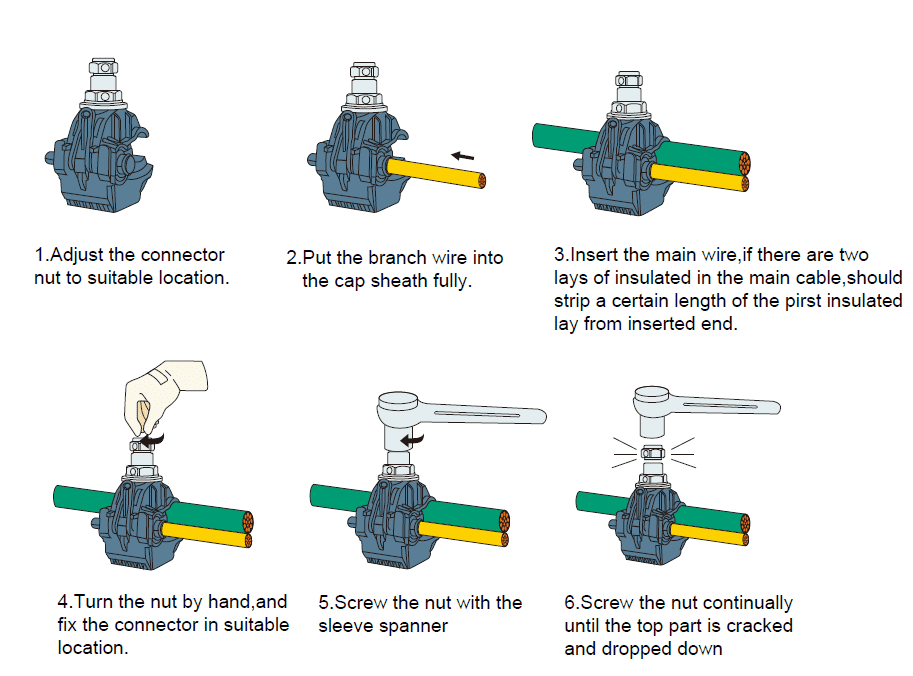
Handle Cables Carefully:
Avoid leaving scratches or embedding particles (e.g., semi-conductive debris) into insulation.
Remove sharp edges or burrs after crimping hardware.
Use Proper Tools:
Torque Wrench Only: Tighten nuts evenly until they break off, ensuring consistent pressure.
Insulated Gloves & Tools: Mandatory for live-line installations.
Post-Installation Validation
Insulation Resistance Test:
Measure the main cable’s insulation resistance to confirm compliance with safety standards.
Visual Inspection:
Verify torque nut breakage and proper alignment of cables.
Ensure no gaps or misalignments in the IPC housing.
Common Pitfalls to Avoid
1. Subpar Workmanship
Rushed Stripping: Incorrect stripping lengths or damaged insulation create weak points.
Ignoring Environmental Controls: Moisture or dust ingress during installation leads to long-term failures.
2. Tool Misuse
Open-End Wrenches: These can slip and damage the clamp. Always use a socket wrench.
Reusing IPCs: These are single-use devices. Disassembling them compromises integrity.
3. Skipping Tests
DC Withstand Voltage Tests: These create reverse electric fields, damaging insulation. Opt for AC testing instead.
Why Professional Installation Matters
Reduced Failure Rates: Certified teams minimize errors in cable prep, alignment, and sealing.
Long-Term Reliability: Properly installed IPC Cable Clamp lasts for decades with minimal maintenance.
Final Reminders
Use Certified Materials: Ensure cables and insulation piercing connectors meet national standards.
Train Personnel: Only skilled technicians should handle IPC installations.
Prioritize Safety: Always de-energize systems when possible, or use insulated gear for live work.
Following these precautions can mitigate risks and ensure your IPC cable clamps deliver safe, efficient, and durable performance. For complex projects, consider partnering with certified professionals to guarantee optimal results.
Need Reliable IPC Solutions? Explore our range of high-quality, compliant cable clamps designed for hassle-free installations. Contact us now!